Powering Up Production: Best Bottle Filling Machines for Startups in 2025
The PET Blow Moulding industry has witnessed exponential growth due to the increasing demand for packaged drinking water, beverages, and pharmaceutical products. However, running a PET blow machine comes with significant operational costs. If you’re in the packaging industry, reducing the running costs while maintaining efficiency can make your business more profitable.
This guide outlines practical tips to improve PET blow machine efficiency and reduce expenses — without compromising product quality.
Why PET Blow Machine Efficiency Matters
A poorly optimized PET blow machine consumes more electricity, wastes raw material, and reduces production output. On the contrary, a highly efficient setup ensures:
-
Consistent bottle quality
-
Lower energy bills
-
Reduced machine wear and tear
-
Increased productivity
Therefore, taking proactive steps to optimize your machine is not just a recommendation; it is a necessity for sustainable growth.
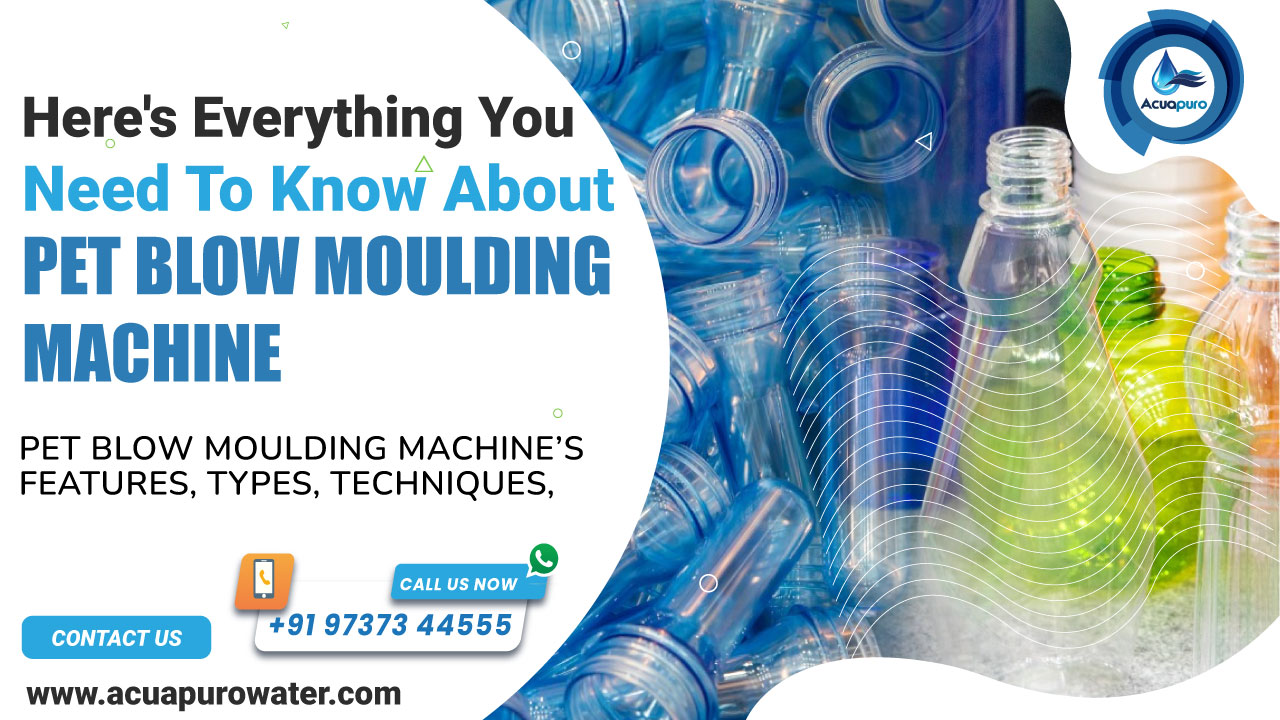
Tips to Reduce Running Costs Without Sacrificing Quality
Here are key strategies that can significantly lower operational costs and enhance overall machine performance.
1. Optimize Heating Zones
Use Infrared Sensors for Real-Time Monitoring
Preform heating is the most energy-intensive part of the PET blowing process. However, many operators overlook the importance of heater calibration. By optimizing the temperature settings of each zone, you can avoid overheating and save on power consumption.
Install infrared sensors or pyrometers to monitor the temperature in real-time. This allows for immediate adjustments and ensures the preform receives just the right amount of heat.
Prevent Uneven Heating
Uneven heating causes bottle defects, leading to material wastage and downtime. Regular maintenance and sensor checks prevent this, resulting in more uniform and efficient production.
2. Schedule Preventive Maintenance
Downtime is Expensive
Unplanned downtime is one of the hidden costs of operating PET blow machines. To minimize this, adopt a preventive maintenance schedule. It may include checking:
-
Air leakage in pneumatic systems
-
Wear and tear in servo motors
-
Oil levels in hydraulic systems
-
Mold alignment and cooling channels
By doing so, you prevent breakdowns and extend the machine’s operational life.
Replace Worn-Out Parts Proactively
Even small components, if neglected, can cause major failures. Always maintain an inventory of critical spare parts to reduce lead time and production loss.
3. Use High-Quality Preforms and Molds
Low-grade preforms often require more heat to mold properly. This not only increases energy usage but also lowers machine output due to frequent stoppages.
Partner With Reliable Suppliers
Choose preforms from certified suppliers and invest in CNC precision molds that offer consistent thickness and shape. These factors ensure smoother machine operations and faster cycle times.
4. Reduce Compressed Air Consumption
Install Air Recovery Systems
PET blow machines consume large volumes of high-pressure air. But did you know that up to 40% of this air can be recovered and reused?
Installing an air recovery system can significantly reduce your energy bills. Moreover, using low-pressure air for pre-blowing and stretching further optimizes air usage.
Check for Leakages Regularly
A small air leak may seem harmless but can cost you hundreds of dollars every month. Conduct periodic audits using ultrasonic leak detectors and plug the leaks immediately.
5. Automate Wherever Possible
Automation isn’t just a trend — it’s a cost-saving tool.
Benefits of Automation in PET Blow Lines
-
Reduced human error
-
Lower labor costs
-
Consistent quality
-
Faster cycle times
From preform loading to bottle ejection, automation boosts throughput while minimizing waste.
Hidden Tips That Make a Big Difference
Sometimes, the smallest tweaks make the biggest impact. Here are a few additional suggestions:
Maintain Correct Machine Alignment
Misaligned molds or stretch rods cause mechanical stress, leading to early wear. Make sure your technicians check alignment weekly.
Insulate Heating Chambers
Insulation keeps the heat in and reduces the load on your heaters. This small investment can result in significant energy savings over time.
Analyze Production Data
Use IoT-based monitoring systems to collect data on cycle time, air usage, and electricity consumption. This insight can reveal inefficiencies that would otherwise go unnoticed.
What Are the Long-Term Benefits of PET blow machine?
By implementing these strategies, manufacturers not only save money but also improve brand reputation through consistent quality and timely delivery. Additionally, reducing energy and air consumption lowers your carbon footprint, a growing concern in today’s environmentally conscious market.
Energy-Efficiency = Market Competitiveness
Customers prefer working with companies that are efficient, reliable, and sustainable. Optimizing your PET blow machine can become your competitive edge.
Final Thoughts: Improve PET Bottle Quality: Pet Blow Machine Best Use
Enhancing your PET blow machine efficiency is not a one-time task. It requires continuous monitoring, periodic upgrades, and a culture of operational excellence. However, the benefits — reduced costs, better quality, and improved customer satisfaction — far outweigh the efforts.
By following these actionable tips, your business can thrive in a competitive market while minimizing running costs. It’s time to shift from reactive maintenance to proactive optimization.
Read More: Maximize Output: Choosing Your Best Pet Blow Machine | Start PET Blow Business Low-Cost 🤑💸🔥 2025